Bodging with style
- Ian Ryder
- Mar 7, 2022
- 4 min read
Updated: Apr 8, 2022
For as long as I can remember, I have been happy to attempt all kinds of DIY, with results ranging from the passable to the disastrous ('is there meant to be blue water coming through the ceiling?"). But in anticipation of having more time on my hands, I decided that perhaps woodwork really could be my long lost forte...
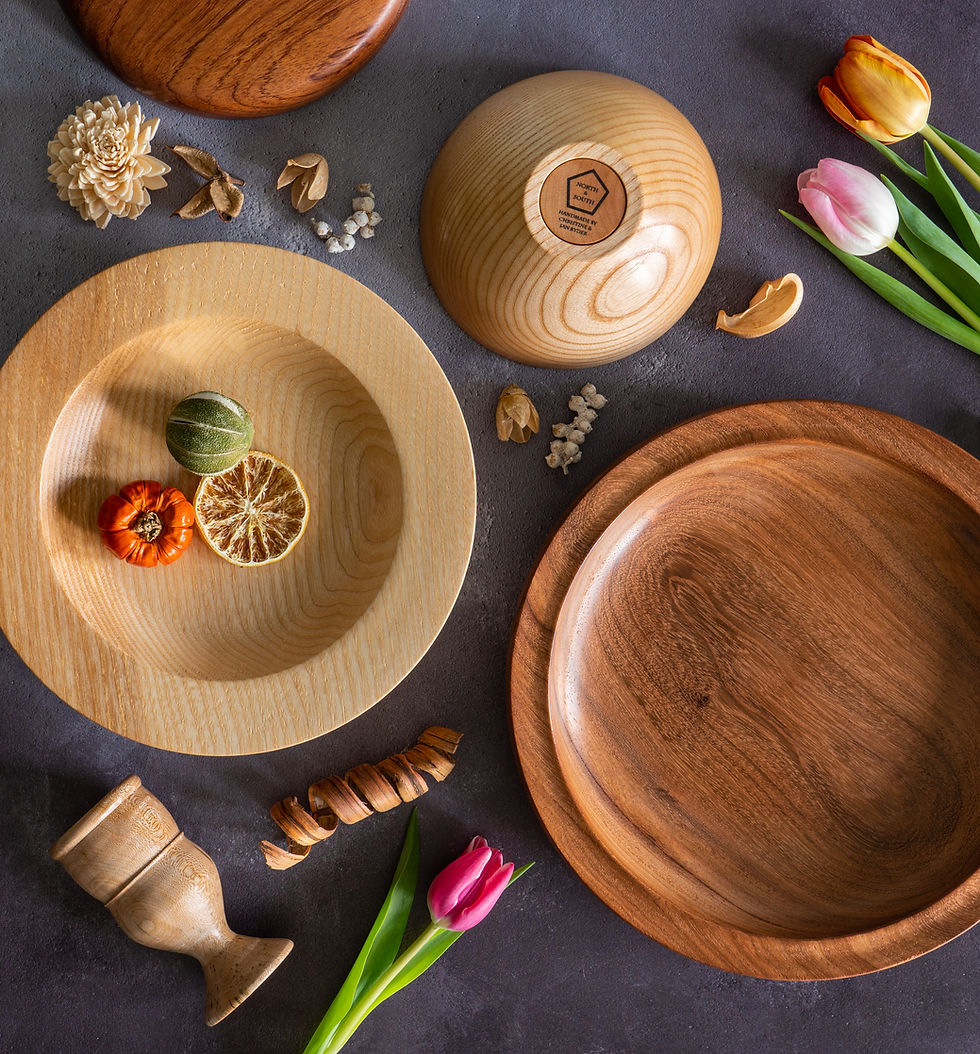
Of course, no self respecting man with a shed (or in my case a share of a garage) could hold his head up high without a good selection of manly tools. Firmly believing in the old adage 'the one who dies with the most tools wins', I set out to replace my long-abused collection of random implements with a proper set of decent woodworking paraphernalia. It's obvious, isn't it - good tools guarantee good results! Ok, maybe not. But at least I could start following my dad's guidance and buy the best I could afford - as it will be cheaper in the end. Had I paid attention to him around fifty years ago, I would probably be a lot better off... But who ever heard of listening to their parents?
In my case, it all started with a quality workbench - and I have not regretted it. This one is Scandinavian - they know a thing or two about wood and stuff, having honed their skills as Vikings making boats, swords and axes with which to pillage their nice friendly neighbours. The main thing about such a bench is that it is rock solid - whether working on the bench top or with wood held in the vice, nothing is going to move however hard your bash it - so planing, hammering and sawing all become so much easier and more predictable.

When working on the bench, it helps to have your tools ready to hand - so that means putting up some kind of tool rack, or 'till' on the wall above the bench. Mine is far from perfect but it does hold a lot of stuff in very little space (the one thing I really lack is a good sized workshop, but having seen videos of Japanese blokes making masterpieces while sitting on the floor in something the size of a downstairs loo, I don't feel hard done by):

Now suitably armed with decent hand tools, it was time to bring in the big guns (provided that they were quite small)... In my case, this meant a bandsaw and a woodturning lathe. Space constraints again dictated that I couldn't get the full machinery monty, such as a table saw, router station and jointer/planer - so these two seemed the best combination to help me do as much as possible:

The bandsaw is a mini machine, but built to a high spec by Axminster and very capable, while the Record Power lathe has all the features you might want (especially the rotating headstock, so I can turn larger bowls and platters).
So with my man cave now suitably equipped I have set out on my odyssey of craftsmanship. Early on, this meant making 'jigs' of various kinds to help with simple tasks like accurate sawing, planing and routing. The most unusual example of these is probably the bike stand I made so I can service my bikes in the dry of the garage. This saved quite a bt of money by using a simple but strong bike clamp and marrying this to a sturdy wooden arm that can be locked in place in the end vice of the workbench (and as I said, stuff in that bench does not move)... Along with a handlebar stay built also from wood, I now have a very workable solution for bike maintenance.

Eventually, after months of setting up, I could finally turn my hand to making things other than tools and an unholy mess. First step - woodturning... Having realised that with a lathe and sharp woodworking tools there was an unlimited list of things that could go disastrously awry, I decided to enrol on a course to learn what not to do before I went and did it. Amazingly, I actually produced something that looked vaguely bowl shaped. If you are interested, I can certainly recommend Les and Martin at the woodturning shop in Alton, Hampshire - their tuition and facilities are excellent and I really enjoyed my day with them.
Back home, I have since made half a dozen bowls and am slowly getting more accomplished at the turning and finishing process - far from expert, but enough to reach my aspired degree of 'bodging with style'. Fusing my photography and woodwork, I made the flat lay at the start of this blog to show off some of what I've made so far.
Before you start thinking I might actually be quite good at this, I should confess that the bowl at the top left of that picture (made from a lovely rich wood called 'Bubinga') is in that position so you can't see the mistakes I made on the other side of it. In fact, not only is that bowl very poorly finished, it is also turned so thin that you can see through the bottom of it if you hold it up to the light! Several lessons learned there - though I do have a cunning plan to rescue it by insetting another piece of complementary wood and re-turning the bowl. If I succeed in that, I may do another blog on that subject one day.
My next planned adventure is to attempt spoon carving with green wood, axes and knives. What could possibly go wrong? Think I had better go on another course first...
Kommentare